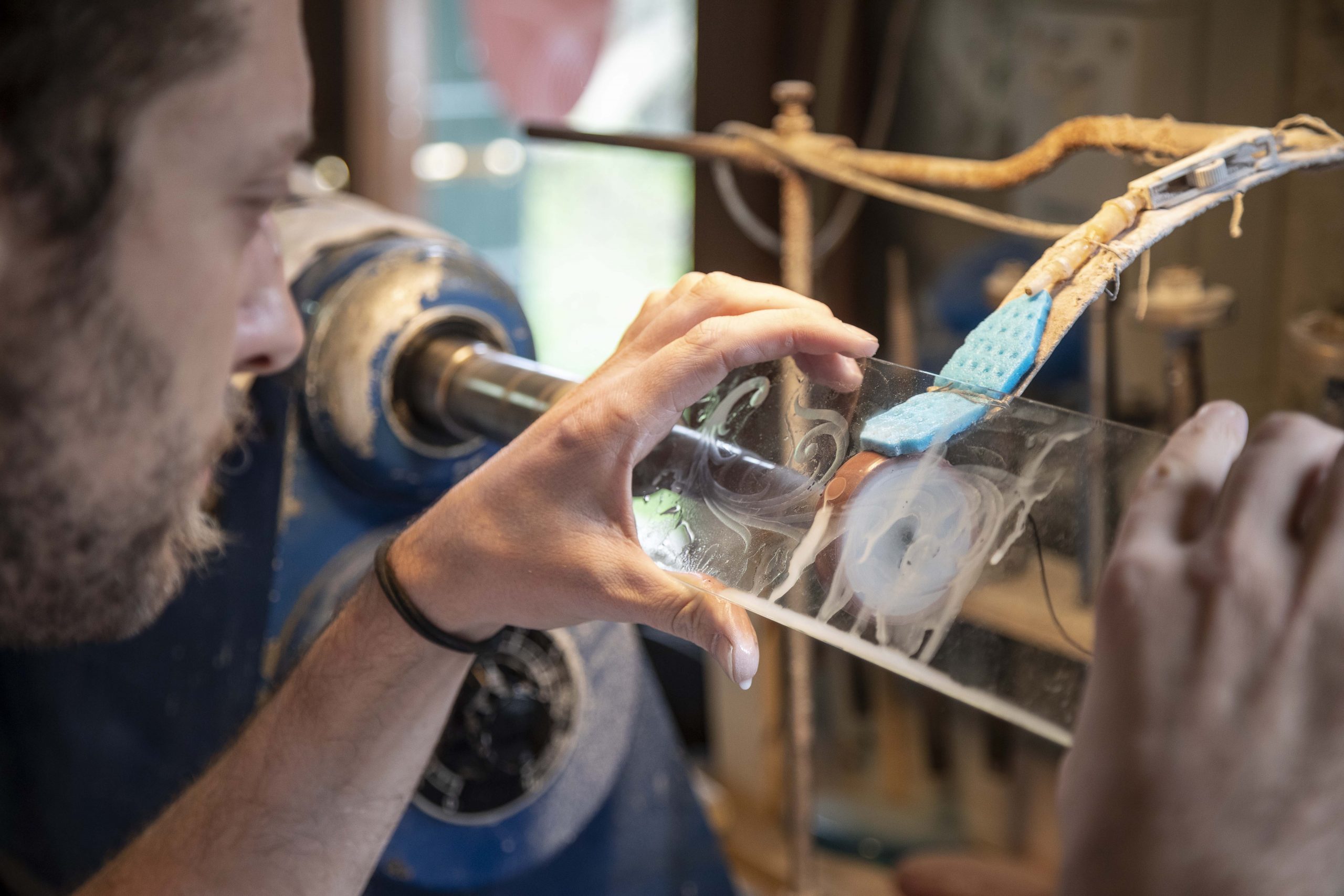
Barbini Specchi Venenziani: the spectacular art of glass engraving
The history of the Barbini family goes along with the tradition of Venetian mirrors, which dates back to the 16th century. The brothers Giovanni and Vincenzo Barbini, with the support of their children, still nowadays personally carry out all the stages of processing using the traditional techniques of the craft.
In 2018 they received the accolade MAM – Master of Arts and Crafts, promoted by the Cologni Foundation in collaboration with Alma. They took part in Homo Faber Event 2022 in Venice, exhibiting an extraordinary monumental mirror in homage to the Empire of the Rising Sun.
What is your story and how was “Barbini Mirrors Veneziani” born?
AAV Barbini Srl is the oldest Murano company still in business, with regards to the art of Venetian mirrors.
The Barbinis have been present in Murano since the second half of the 16th century. In 1658, by order of the Council of Ten, our name was inscribed in the “Golden Book of the Magnificent Community of Murano”, known as the book of the glass nobility of the island.
Over the centuries the members of the family worked in the various sectors of artistic glass production, such as in the chandeliers, beads, conterie and various objects, specializing in particular in the manufacture of Venetian mirrors, contributing to the prestige and quality to the Serenissima and the island’s artisanal production.
The earliest news about our family dates back to the seventeenth century. In 1665 some glass masters were secretly taken to France, to the court of Louis XIV, to start a local production of Venetian mirrors. Among them is Gerolamo Barbini, who collaborated at the “Manufacture Royale des glaces de miroirs”, in the Parisian area of Saint-Antoine.
During the nineteenth century almost all the members of our family worked as “conzadori” masters, providing consultancy to the major factories in Murano.
In the twentieth century, Nicolò and his brother Guglielmo Barbini resumed the processing of Venetian mirrors in Murano, by then almost completely forgotten, thus reinterpreting a priceless heritage of techniques and secrets. Nicolò passed on this legacy to his sons Vincenzo and Giovanni, who would continue the long family tradition up to the present day.
In 1927 Nicolò Barbini founded his first company for artistically engraved glass, with which his brother Guglielmo, also an engraver, collaborated, immediately distinguishing himself for the elegance and refinement of the mirrors produced. After only two years of activity, in 1929, he was awarded the First Grade Gold Medal at the Exhibition in Florence. In 1985 Vincenzo and Giovanni became the owners of the company, which currently employs the work of three generations of expert craftsmen. All stages of processing – the design, cutting, grinding, engraving, silvering and assembly – are carried out exclusively in Murano, and personally followed by us brothers and our respective children, Nicola, Marco and Giovanna, Pietro, Andrea and Filippo, capable of continuously reinterpreting an inestimable family heritage of techniques and secrets.
How does the process of conception, design and realization of your work take place?
We can summarize the process of making one of our pieces with the word “dialogue”: a continuous dialogue between us, between the artisans we work with and the designer or artist. And it is precisely from the comparison with the skills and experiences of the other person that our works are born.
How important is the link with the city of Venice and the island of Murano for your work?
Our activity as mirror makers is necessarily linked to our territory, and the name of our product already says it with absolute and unequivocal clarity: Venetian Mirrors.
We know well that mirrors and glass were not invented in Murano or Venice, but right here the art of glass has developed like nowhere else. Here were invented processing techniques, tools, machinery, types of glass, applications and styles, and the same “Venetian mirror”: a spectacular object requested by the crowned heads of all Europe, which initially differed from all the others for the quality, the clarity and perfection of the mirror surface; later for the frames decorated with straws, leaves and flowers in colored glass, or with elements in engraved glass, while still throughout Europe the frames were made of sealing wax, wood and various metals.
What is your source of inspiration?
Our sources of inspiration are always linked to tradition, with a necessary adaptation to the taste of customers, and the support of young designers.
There is always a renewal in production, linked to the market and changing tastes. But often it is a matter of updating only the combination of colors or a few other elements, leaving the fundamental traits of tradition intact. For this reason, we now have over 1000 models.
How do you combine the strong bond with tradition with the ability to always innovate decorations and styles?
Today we can say that in our work the combination of tradition and innovation is expressed by leaving room for new ideas and proposals, trying to see the “new” as an enrichment of our knowledge and technical skills.
We, as an older generation of artisans, usually look at new technologies with a suspicious mind, without thinking that these could instead enrich our knowledge, enhance the techniques we already use and, consequently, make the product even more unique.
Our children have helped us a lot: joining the company, they have brought new vitality and energy to the production, the desire to experiment with new silvering and engraving techniques, the introduction of new machinery, such as the very modern water jet, which we are the only ones to own in Murano, an oven for melting glass is installed.
Do you carry out teaching activities within your company? Are you available to welcome young people for training apprenticeships?
We have always trained young people to make them learn the trade, also hiring many of them in the company: now more than ever since the company is in the hands of our children and grandchildren. Furthermore, in recent years, we have welcomed some young people for school-work alternation, trying to make them aware of all the stages of the Venetian mirror manufacturing process.
What are the plans for the future of your company?
Our will is to continue to enhance Murano glass and make the world of Venetian mirror processing and its innumerable potentials known to the world; as well as enhancing collaboration as a founding value, a sine qua non for experimenting with new worlds and experiences, which is one of the secrets of the success of Murano glass.
Barbini Specchi Veneziani
Calle Dietro gli Orti, 7 – Murano (Venice)
www.aavbarbini.it
info@aavbarbini.it
Ph: +39 041.739 518
25 Settembre 2022